Máy móc là một phần không thể tách rời khỏi cuộc sống hàng ngày, là công cụ giúp con người đạt được những bước tiến xa trong cuộc sống. Tuy nhiên, tất cả chúng đều được cấu thành từ các chi tiết máy rất nhỏ qua nhiều bước gia công khác nhau. Vậy gia công chi tiết máy cụ thể là gì? Tất cả sẽ có trong bài viết này.
Mục lục
1. Khái niệm gia công chi tiết máy
Gia công chi tiết máy là một quá trình gia công đòi hỏi nhiều công đoạn trong gia công chi tiết cơ khí, con người vận hàng máy móc để tạo ra các sản phẩm theo yêu cầu. Để hiểu hết về gia công chi tiết máy trước hết bạn cần nắm được chi tiết máy là gì?
2. Gia công chi tiết máy là gì?
Chi tiết máy là những thành phần cơ bản cấu thành nên các thiết bị và máy móc. Mỗi chi tiết máy đóng vai trò quan trọng với nhiệm vụ và chức năng riêng, tạo nên sự hoạt động của các thiết bị và máy móc. Chúng thường được sản xuất từ nhiều loại vật liệu khác nhau, nhưng phần lớn là kim loại.
Gia công chi tiết máy là một quá trình gia công gồm nhiều phương pháp kết hợp cắt, gọt, rèn, đút, mài,.. từ những phôi thô thành chi tiết cụ thể, riêng lẻ, chi tiết này ứng dụng trong máy móc gọi là gia công chi tiết máy hay còn gọi là gia công chi tiết cơ khí. Sau khi gia công chúng sẽ có kích thước và kết cấu như bản vẽ thiết kế. Để máy hoạt động hiệu quả mang lại năng suất cao đòi hỏi các chi tiết cần đảm bảo về độ chính xác cũng như các đặc điểm cần thiết.
Gia công chi tiết máy là quá trình biến đổi từ phôi thông qua các phương pháp cơ khí như nung, hàn, đục, mài… để tạo ra các hình dạng và kích thước cụ thể. Quá trình này thường đòi hỏi sự chính xác và đáng tin cậy để đảm bảo các chi tiết hoạt động một cách hiệu quả. Ứng dụng của gia công chi tiết máy rất đa dạng và phổ biến trong nhiều lĩnh vực.
Gia công chi tiết máy là quá trình biến đổi từ phôi thông qua các phương pháp cơ khí như nung, hàn, đục, mài… để tạo ra các hình dạng và kích thước cụ thể. Quá trình này thường đòi hỏi sự chính xác và đáng tin cậy để đảm bảo các chi tiết hoạt động một cách hiệu quả.
Chi tiết máy là những phần tử cấu tạo đầu tiên hoàn chỉnh của máy. Mỗi chi tiết sẽ có hình dáng, kích thước, nguyên lý làm việc và tính năng khác nhau.
Bạn có thể thấy bất kỳ máy móc nào dù đơn giản hay phức đều được cấu thành từ nhiều bộ phận. Ví dụ máy tiện gồm có: bàn máy, ụ đứng, ụ động, hộp tốc độ, bàn dao, cơ cấu truyền dẫn từ động cơ đến hộp tốc độ,.. trong mỗi bộ phận máy lại gồm nhiều chi tiết. Ví dụ ụ đứng của máy tiện gồm có: ụ, trục chính, ổ trục, bánh răng, trục,..
Chi tiết máy có thể làm bằng phi kim: nhựa, cao su, composite. Kim loại như: đồng, sắt, thép, nhôm, inox. Trên bản vẽ thường có 2 loại, 1 là bản vẽ chi tiết, 2 là bản vẽ lắp ghép. Người gia công họ chỉ cần bản vẽ chi tiết, người chế tạo máy cần bản vẽ lắp ghép.
Ứng dụng của gia công chi tiết máy rất đa dạng và phổ biến trong nhiều lĩnh vực. Từ các chi tiết trong ô tô, máy lạnh đến tủ lạnh, chúng đều là sản phẩm của quá trình gia công chi tiết máy. Nếu không có công nghệ hiện đại này, sản xuất các thiết bị này sẽ tốn kém và không hiệu quả như hiện nay.
3. Quy trình gia công chi tiết máy móc cơ khí
Gia công chi tiết máy là ứng dụng phổ biến của gia công cơ khí. Quy trình này đòi hỏi nhiều bước có liên quan chặt chẽ và đồng bộ với nhau. Dưới đây là quy trình cụ thể trong việc gia công các chi tiết máy móc cơ khí:
Bước 1: Tạo bản vẽ thiết kế cơ khí
Bước đầu tiên trong quy trình gia công chi tiết máy móc cơ khí là tạo ra bản vẽ thiết kế chi tiết cho sản phẩm. Bản vẽ này không chỉ là một hình ảnh đơn thuần, mà còn là một tài liệu có những thông tin kỹ thuật chi tiết.
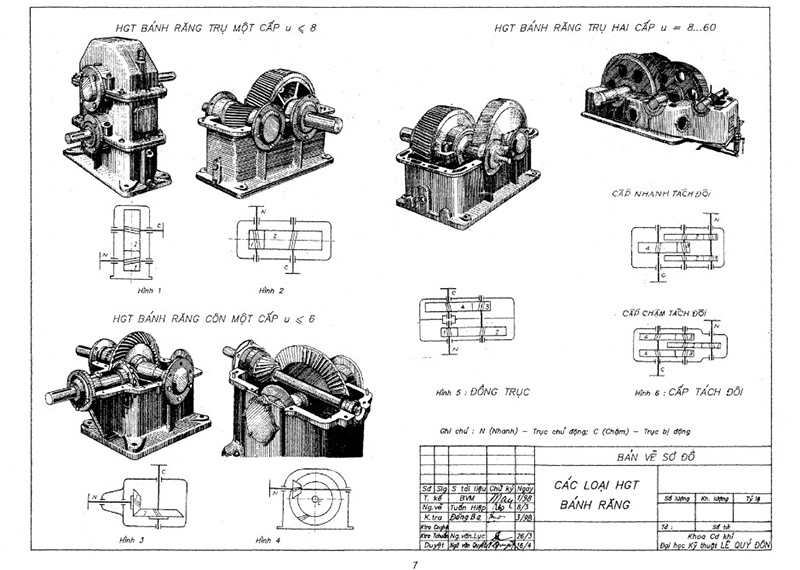
Trong bản vẽ, các thông số kỹ thuật của sản phẩm được định rõ, gồm kích thước, tổng thể, hình dạng cụ thể và các yếu tố khác như là vật liệu, phương pháp gia công. Những thông tin này giúp cho những kỹ sư nắm rõ hơn về sản phẩm và biết cách tiến hành gia công. Đây được xem là một bước đầu quan trọng trong quá trình, vì nó đặt nền tảng cho những bước tiếp theo.
Bước 2: Xác định phương thức sản xuất
Bước thứ hai trong quá trình gia công chi tiết cơ khí là xác định phương thức sản xuất. Và có ba phương thức chính:
Sản xuất chiếc: Với phương thức này thì thường tập trung vào việc sản xuất một chi tiết máy duy nhất tại một thời điểm. Mỗi chi tiết máy đều được chăm sóc kỹ lưỡng, đảm bảo rằng nó đáp ứng được các yêu cầu kỹ thuật.
Sản xuất hàng loạt: Phương thức này cho phép sản xuất nhiều chi tiết máy cùng một lúc, tất cả đều có cùng kích thước, hình dạng và dung sai. Điều này rất thích hợp cho việc sản xuất hàng loạt các sản phẩm giống hệt nhau, giúp tăng hiệu suất và giảm chi phí.
Sản xuất hàng khối: Phương thức này cũng cho phép sản xuất hàng loạt, nhưng với mức độ chính xác cao hơn. Tất cả các chi tiết máy đều có cùng kích thước, hình dạng và dung sai cao. Điều này thích hợp cho việc sản xuất hàng loạt các sản phẩm yêu cầu độ chính xác cao.
Việc lựa chọn phương thức sản xuất phù hợp sẽ phụ thuộc vào nhiều yếu tố, bao gồm yêu cầu về sản phẩm, số lượng cần sản xuất, và các yếu tố khác như thời gian, chi phí. Mỗi phương thức đều có ưu và nhược điểm riêng, do đó việc lựa chọn đúng phương thức sản xuất là rất quan trọng.
Bước 3: Chọn phôi và phương pháp chế tạo phôi
Sau bước xác định phương thức sản xuất thì sẽ tới bước chọn phôi và chế tạo phôi.
Phôi cần được đảm bảo cơ tính của gia công. Kích thước của phôi được xác định dựa trên lượng dư gia công và cần đảm bảo rằng chi phí của vật liệu, chi phí gia công được giảm thiểu. Điều này giúp nâng cao năng suất và giảm giá thành sản phẩm.
Vật liệu phôi có thể đa dạng từ kim loại, hợp kim cho đến vật liệu phi kim, và nó sẽ phụ thuộc vào thực tế sản xuất.
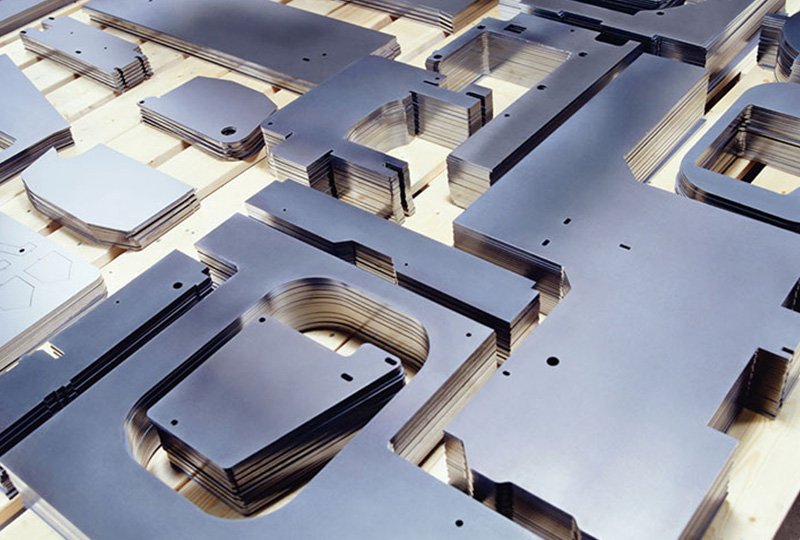
Có nhiều phương pháp chế tạo phôi phổ biến, bao gồm:
Phương pháp đúc: Với phương pháp này thì phôi sẽ được tạo hình bằng cách đúc khuôn cát, kim loại, đúc ly tâm, áp lực và nhiều phương pháp khác. Quá trình này tạo ra hình dạng cơ bản của phôi.
Gia công áp lực: Các phương pháp như cán, rèn, dập thể tích, và nhiều phương pháp khác được sử dụng để biến đổi hình dạng của phôi. Quá trình này thường được sử dụng khi cần tạo ra hình dạng phức tạp hoặc độ chính xác cao.
Gia công hàn: Phương pháp này được sử dụng khi cần kết nối các phần khác nhau của phôi lại với nhau.
Việc lựa chọn phương pháp chế tạo phôi phù hợp sẽ phụ thuộc vào nhiều yếu tố, bao gồm yêu cầu về sản phẩm, số lượng cần sản xuất, và các yếu tố khác như thời gian, chi phí.
Bước 4: Xác định thứ tự các bước
Bước thứ tư trong quy trình gia công chi tiết máy móc cơ khí là xác định thứ tự các bước gia công chi tiết. Bước này được thực hiện dựa trên bản vẽ thiết kế và yêu cầu kỹ thuật của sản phẩm. Thứ tự các bước cần phải đảm bảo về hình dạng, kích thước và độ chính xác của chi tiết máy được tạo ra đúng với yêu cầu.
Việc xác định thứ tự các bước gia công là một phần quan trọng của quy trình, đòi hỏi sự hiểu biết về cả kỹ thuật và quản lý sản xuất. Mỗi quyết định ở bước này có thể ảnh hưởng đến chất lượng sản phẩm cuối cùng và hiệu suất của quy trình.
Bước 5: Lựa chọn máy móc, thiết bị phù hợp cho các nguyên công
Tiếp theo là việc lựa chọn máy móc và thiết bị phù hợp cho các nguyên công. Ở bước này, các kỹ thuật viên cần phải hiểu rõ về các dụng cụ đo lường cần thiết cho quá trình tính toán và kiểm tra độ chính xác của chi tiết gia công trong suốt quá trình. Việc lựa chọn máy móc và thiết bị phù hợp không chỉ ảnh hưởng đến chất lượng của sản phẩm cuối cùng, mà còn ảnh hưởng đến hiệu suất và hiệu quả của quá trình sản xuất. Do đó, việc lựa chọn đúng thiết bị và dụng cụ đo lường là rất quan trọng trong quy trình sản xuất cơ khí.
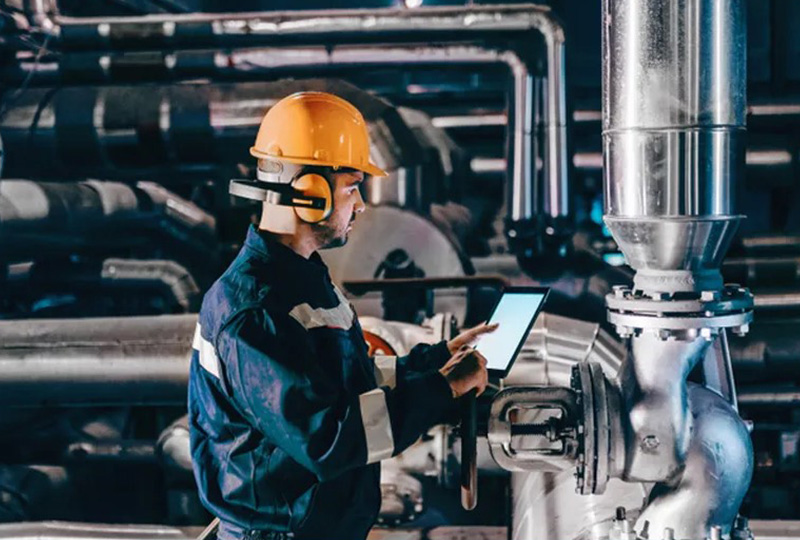
Bước 6: Xác định lượng dư gia công cho các bước
Tiếp theo là bước xác định lượng dư gia công cho các bước. Lượng dư gia công là phần vật liệu dư thừa cần được loại bỏ từ phôi trong quá trình gia công. Việc xác định lượng dư gia công cần phải tuân theo các yêu cầu sau:
Đảm bảo độ chính xác gia công: Lượng dư gia công cần đủ để cho phép các bước gia công sau có thể đạt được độ chính xác cần thiết. Nếu lượng dư gia công quá ít, có thể không thể đạt được độ chính xác yêu cầu. Ngược lại, nếu lượng dư gia công quá nhiều, có thể dẫn đến việc phải thực hiện thêm các bước gia công không cần thiết.
Giảm chi phí gia công: Lượng dư gia công càng ít, chi phí gia công càng thấp. Điều này là do việc loại bỏ vật liệu dư thừa đòi hỏi thời gian, năng lượng và nguyên liệu. Do đó, việc giảm lượng dư gia công có thể giúp tiết kiệm chi phí.
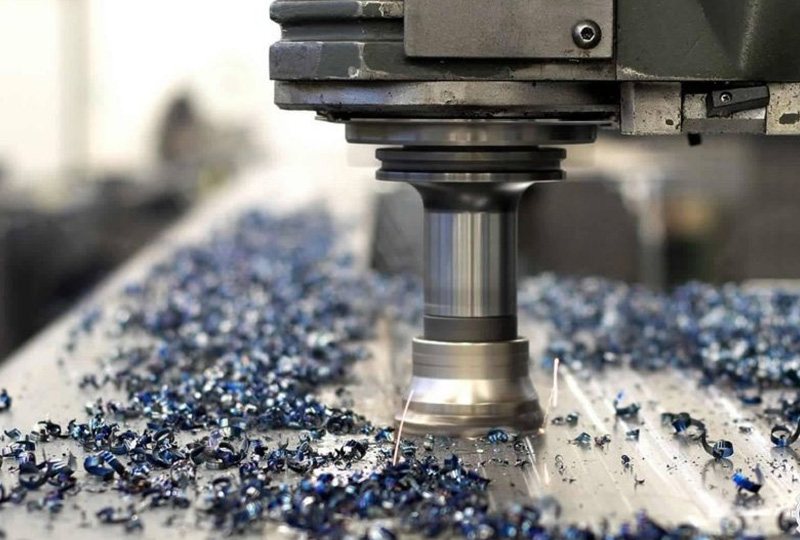
Giảm thời gian gia công: Giống như việc giảm chi phí, việc giảm lượng dư gia công cũng có thể giúp giảm thời gian gia công. Thời gian cần thiết để loại bỏ vật liệu dư thừa có thể được sử dụng cho các bước gia công khác, do đó tăng hiệu suất sản xuất.
Việc xác định lượng dư gia công là một phần quan trọng của quy trình gia công chi tiết máy cơ khí, đòi hỏi sự cân nhắc kỹ lưỡng và hiểu biết về quy trình gia công cụ thể. Mỗi quyết định ở bước này có thể ảnh hưởng đến chất lượng sản phẩm cuối cùng và hiệu suất của quy trình sản xuất.
Bước 7: Xác định chế độ cắt trong các nguyên công, các bước
Sau khi đã xác định lượng dư gia công cho các bước thì tiếp theo là xác định chế độ cắt cho từng nguyên công và từng bước gia công. Ở bước này, kỹ thuật viên cần phải tính toán và lựa chọn chế độ gia công cơ khí phù hợp với vật liệu đang được sử dụng, để đảm bảo rằng từng nguyên công được thực hiện một cách chính xác, giúp sản phẩm cuối cùng đạt được độ chính xác cao nhất.
Có nhiều phương pháp cắt khác nhau có thể được sử dụng, bao gồm tiện, phay, khoan, bào, và nhiều phương pháp khác. Chế độ cắt được xác định bởi các trị số như chiều sâu cắt (t), lượng chạy dao (s), tốc độ cắt (v), và công suất cần thiết (N).
Việc xác định chế độ cắt phù hợp là một phần quan trọng của quy trình, vì nó ảnh hưởng trực tiếp đến chất lượng của sản phẩm cuối cùng. Mỗi quyết định ở bước này cần phải được cân nhắc kỹ lưỡng, dựa trên hiểu biết về vật liệu, nguyên công, và yêu cầu kỹ thuật của sản phẩm. Việc này đòi hỏi sự hiểu biết sâu sắc về cả kỹ thuật và quản lý sản xuất.
Bước 8: Chọn đồ gá cho từng nguyên công
Bước thứ tám trong quy trình sản xuất cơ khí là chọn đồ gá phù hợp cho từng nguyên công. Đồ gá bao gồm các công cụ, kẹt, mẫu gá và các phụ kiện khác, được sử dụng để giữ chắc và cố định phôi trong suốt quá trình gia công. Việc chọn đồ gá phù hợp đòi hỏi sự hiểu biết về từng phương pháp gia công cụ thể và yêu cầu của sản phẩm. Đồ gá cần phải đảm bảo rằng phôi được giữ chắc chắn và ổn định trong suốt quá trình gia công, để đảm bảo độ chính xác và an toàn.
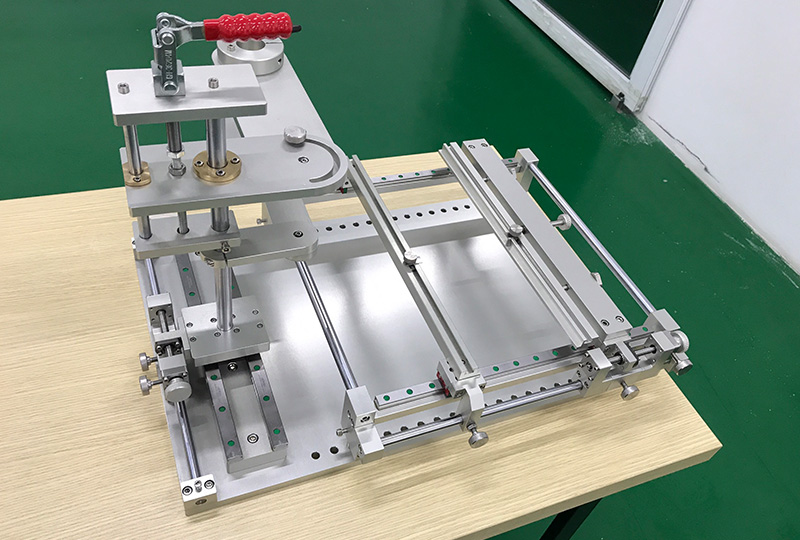
Bước 9: Tiến hành quy trình gia công cơ khí chính xác
Tiếp theo là bước tiến hành quá trình gia công cơ khí chính xác. Ở bước này, kỹ thuật viên sẽ sử dụng các máy móc hiện đại để thực hiện công việc gia công sản phẩm. Các máy móc được sử dụng trong quá trình này có thể bao gồm: máy tiện, máy phay, máy bào, máy khoan,…
Qua quá trình gia công này, chi tiết máy sẽ được tạo ra với độ chính xác cao, đáp ứng được yêu cầu kỹ thuật và chất lượng của sản phẩm cuối cùng. Việc sử dụng các máy móc hiện đại giúp tăng hiệu suất và chất lượng của quá trình sản xuất, đồng thời giảm thiểu thời gian và chi phí.
Bước 10: Kiểm tra sản phẩm sau quy trình gia công cơ khí chính xác
Bước cuối cùng trong quy trình gia công chi tiết máy cơ khí là kiểm tra chất lượng sản phẩm sau khi gia công. Ở bước này, sản phẩm sẽ được kiểm tra kỹ lưỡng để đảm bảo rằng nó đáp ứng được tất cả các yêu cầu về kích thước, độ nhám bề mặt, biên dạng, và các yêu cầu khác.
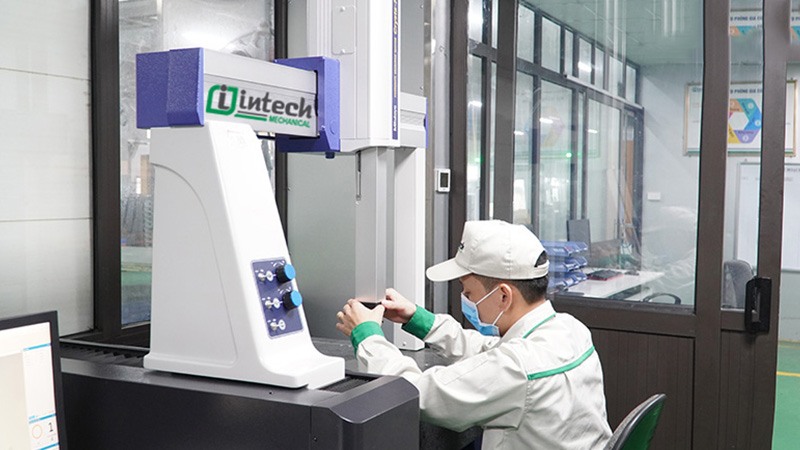
Qua quá trình kiểm tra này, kỹ thuật viên có thể đảm bảo rằng sản phẩm cuối cùng đáp ứng được tất cả các yêu cầu về chất lượng và độ chính xác. Nếu có bất kỳ sai sót nào được phát hiện, họ có thể điều chỉnh quy trình gia công để khắc phục và cải thiện chất lượng sản phẩm. Việc này giúp đảm bảo rằng mỗi sản phẩm cuối cùng đều đạt được chất lượng tốt nhất có thể.
4. Các tiêu chuẩn gia công chi tiết máy
Khi gia công chi tiết máy, cần đảm bảo các yếu tố sau:
- Khả Năng Hoạt Động: Chi tiết phải hoạt động chính xác và hiệu quả theo yêu cầu.
- Độ Tin Cậy: Chi tiết cần đảm bảo độ bền và ổn định trong môi trường làm việc.
- An Toàn: Đảm bảo tính an toàn trong quá trình sử dụng và vận hành.
- Công Nghệ: Sử dụng công nghệ tiên tiến và hiện đại để đạt được chất lượng cao.
- Tính Kinh Tế: Tối ưu hóa quá trình sản xuất để giảm chi phí và tăng tính cạnh tranh.
5. Chi tiết máy gồm những loại nào:
Chi tiết có nhiều loại, kiểu dáng và tính năng khác nhau. Nhưng chúng thường được chia thành 2 loại chính sau:
5.1 Chi tiết có công dụng chung
Đây là các chi tiết được sử dụng phổ biến trong nhiều loại máy khác nhau. Nếu cùng loại thì chúng sẽ có công dụng giống nhau và đảm nhận chức năng như nhau. Các chi tiết có công dụng chung là: bu lông, bánh răng, trục, ổ trục, đai ốc, lò xo, puly…
5.2 Chi tiết có công dụng riêng
Đây là các chi tiết chỉ dùng trong một số loại máy nhất định. Hoạt động của các chi tiết này có công dụng riêng liên quan mật thiết đến quá trình làm việc của máy tương ứng. Các chi tiết có công dụng riêng như: khung xe, xe đạp, trục khuỷu, van, cam, bánh tua bin,…
Ngoài ra có các loại chi tiết chỉ sản xuất cho các loại máy móc riêng biệt, tức là chúng có thiết kế không giống với bất cứ chi tiết nào, thường thấy nhất trong ngành chế tạo máy.
![]() | ![]() |
6. Dấu hiệu để nhận biết chi tiết máy là gì?
Dấu hiệu để nhận biết chi tiết máy là có cấu tạo hoàn chỉnh và không tháo rời được ra nữa, chi tiết máy là phần tử có cấu tạo hoàn chỉnh từ các bộ phận cấu thành tạo nên nhiệm vụ chung nhất định.
7. Phương pháp gia công chi tiết máy
Để đáp ứng nhu cầu ngày càng cao của các doanh nghiệp, thì đã có rất nhiều phương pháp gia công cơ khí hiện đại ra đời.
7.1 Các phương pháp gia công truyền thống
Các phương pháp gia công truyền thống là các công nghệ cắt gọt kim loại sử dụng các dụng cụ có độ cứng cao hơn độ cứng của chi tiết gia công (phôi) để bóc tách vật liệu. Để để tạo hình bề mặt cần có một quan hệ tích hợp giữa chuyển động của dụng cụ và chi tiết gia công.
+ Tiện:
Tiện là phương pháp gia công cắt gọt thông dụng nhất, máy tiện chiếm khoảng 25% đến 35% tổng số thiết bị trong phân xưởng gia công cắt gọt.
+ Phay:
Phay cũng là phương pháp gia công khá phổ biến, chiếm khoảng 20% trong tổng số máy công cụ
+ Khoan – Khoét – Doa –Taro:
Khoan là phương pháp cơ bản để tạo lỗ từ phôi đặc và được sử dụng rất phổi biến
Khoét là phương pháp gia công mở rộng lỗ trên các loại máy như Khoan, Tiện, Phay, Doa,…
Doa là phương pháp gia công tinh các lỗ sau khi khoan, hoặc sau khi khoan khoét hoặc Tiện.
Taro là phương pháp gia công ren, thường dùng gia công ren lỗ tiêu chuẩn. Taro có thể gia công ren trụ, ren côn, ren hệ anh và ren hệ met…..
+ Chuốt:
Chuốt là phương pháp gia công khá phổ biến. Dùng để gia công lỗ tròn, lỗ định hình, lỗ then, rãnh xoắn hay mặt phẳng…..
+ Mài:
Mài gồm có các loại như: mài tròn ngoài, mài tròn trong, mài vô tâm, mài tròn có tâm, mài phẳng….
+ Các phương pháp gia công tinh lần cuối: Mài nghiền, mài khôn, đánh bóng,…
+ Các phương pháp gia công không phôi: lăn, ép….
Phương pháp gia công truyền thống
7.2 Các phương pháp gia công tiên tiến
Dựa trên nguồn năng lượng chủ yếu để bóc tách vật liệu có thể chia các phương pháp gia công cơ khí tiên tiến thành 4 nhóm phương pháp cơ bản như sau:
+ Phương pháp cơ khí:
Bao gồm các phương pháp như gia công bằng tia hạt mài, gia công bằng dòng chảy hạt mài, gia công bằng tia nước, gia công bằng tia nước & hạt mài, gia công bằng siêu âm…
Phương pháp cơ khí thường được áp dụng với các vật liệu gia công khó gia công bằng các kỹ thuật truyền thống vì có độ cứng, độ bền, tính giòn cao như: các loại gốm, thủy tinh, vật liệu Composite hay vật liệu hữu cơ…
Những loại vật liệu này đặc biệt thích hợp cho phương pháp gia công theo nguyên lý cơ học và chúng phần lớn là không dẫn điện và vì chúng bị phá huỷ khi cháy, hoá than hay nứt gãy khi gia công bằng nhiệt.
+ Phương pháp điện hóa:
Bao gồm các phương pháp như gia công điện hóa, mài điện hóa, mài xung điện hóa, khoan bằng dòng chất điện phân, khoan bằng mao dẫn, gia công điện phân ống hình…
Các phương pháp gia công không truyền thống theo nguyên lý điện giới hạn trong việc gia công các vật liệu dẫn điện. Các vật liệu khó gia công bằng các phương pháp thông thường chiếm tỷ lệ lớn áp dụng phương pháp này. Tuy nhiên, có một số lượng lớn các ứng dụng có thể lựa chọn vì khả năng của các phương pháp theo nguyên lý điện ít bị mòn dụng cụ khi gia công các chi tiết phức tạp trong một lần chạy dao.
+ Phương pháp hóa:
Bao gồm các phương pháp như gia công quang hóa, phay hóa…
Được ứng dụng rộng rãi do chi phí ban đầu của dụng cụ thấp, gia công bằng phương pháp hoá được sử dụng rộng rãi để sản xuất với giá rẻ các sản phẩm loạt lớn như lò xo lá, lá môtơ điện và mặt nạ ống hình vô tuyến. Vì vật liệu được bóc tách bằng phản ứng hoá học nên không có lực tác động lên chi tiết. Điều này cho phép gia công chi tiết mà không gây biến dạng hay bị phá huỷ.
Hơn nữa, vì hoạt động gia công tiến hành trên tất cả các mặt của chi tiết một cách đồng thời vì vậy năng suất gia công cao.
+ Phương pháp nhiệt điện:
Bao gồm các phương pháp như gia công bằng xung điện, cắt dây xung điện, mài xung điện, gia công bằng dòng điện tử, gia công cắt Laser, gia công bằng Plasma…
Các phương pháp nhiệt nói chung là không bị ảnh hưởng bởi các tính chất vật lý của vật liệu bị gia công do đó chúng thường được áp dụng để gia công các vật liệu đặc biệt cứng hoặc mềm. Vì cơ chế lấy vật liệu là cơ chế nhiệt, chi tiết được dùng có các ứng dụng quan trọng cần được gia công tiếp theo để loại bỏ phần bị ảnh hưởng vì nhiệt.
Phương pháp gia công kim loại hiện đại
8. Các phương pháp và hình thức gia công các chi tiết cơ khí
Ngày nay, để cho ra đời các chi tiết cơ khí (chi tiết máy, thiết bị, khuôn mẫu hoặc các loại sản phẩm khác) thì chúng ta cần phải trải qua nhiều công đoạn và nhiều máy móc để hỗ trợ một cách hiệu quả. Chính vì vậy, chúng ta hãy cùng đi tìm hiểu về các phương pháp trong bài viết sau đây nhé!
8.1 Phương pháp gia công không phôi:
Chủ yếu gồm các phương pháp như đúc, rèn, dập nóng, dập nguội, cán ép… Sản phẩm cho ra từ phương pháp này thường là các khơi phẩm, chúng là chỉ mới được tạo hình sơ bộ, còn thô và độ nhẵn không cao.
8.2 Phương pháp gia công cắt gọt (còn được gọi là gia công có phôi):
gốm các phương pháp như tiện, phay, bào, doa, khoan… Sản phẩm ra đời từ kỹ thuật gia công này sẽ đạt được hình dáng và kích thước yêu cầu của chi tiết, sản phẩm đã có độ nhẵn và độ chính xác khá cao. Đây là một quá trình công nghệ rất quan trọng của ngành công nghiệp chế tạo máy.
Ngoài 2 kỹ thuật gia công cơ khí trên vẫn còn nhiều phương pháp gia công cơ khí rất mới và hiện đại như: gia công tia lửa điện, gia công bằng tia laser hay gia công bằng sóng siêu âm… Tuy nhiên, những phương pháp này vẫn chưa được sử dụng rộng rãi vì những hạn chế về mặt kỹ thuật hoặc do giá thành máy móc quá cao, chưa được ứng dụng rộng rãi ở các đơn vị công xưởng sản xuất.
9. Các hình thức gia công các chi tiết cơ khí thường gặp
Để phân loại các hình thức gia công cơ khí người ta thường dựa vào cách xác định khối lượng kim loại bị cắt khỏi vật liệu thô ban đầu là nhiều hay ít. Nếu số lượng kim loại này bị cắt khỏi chi tiết gia công theo từng lát cắt của các máy công cụ (thường là các máy CNC). Bên cạnh đó, bạn có thể xác định các hình thức gia công cơ khí dựa vào độ nhẵn của bề mặt chi tiết sau khi gia công.
Một số hình thức chính của kỹ thuật gia công cơ khí:
9.1 Gia công thô:
Phương pháp gia công này giúp chi tiết được cắt gọt đi một lượng lớn dư gia công trên phôi nhằm đạt được dạng hình học cơ bản ban đầu mà sản phẩm yêu cầu. Một số chi tiết chỉ yêu cầu gia công thô là đủ vì những sản phẩm này ra đời không đòi hỏi phải có độ nhẵn và độ chính xác cao. Tuy nhiên, trường hợp vật liệu có lượng gia công quá nhiều, đòi hỏi chúng ta phải thực hiện bước phá gia công ban đầu trước khi tiến hành gia công thô.
Dù được gọi là gia công thô nhưng những sản phẩm cũng phải đạt đến độ chính xác và độ nhẵn quy định.
![]() | ![]() |
9.2 Gia công tinh:
Đây là công đoạn được thực hiện sau khi sản phẩm đã được gia công thô ở bước trước. Lượng gia công bị lấy đi ở bước này tương đối ít và mỏng, vì vậy dụng cụ cắt sử dụng trong quá trình gia công tinh được bảo vệ tương đối an toàn. Sản phẩm ra đời có độ chính xác và độ nhẵn cao hơn so với gia công thô.
![]() | ![]() |
9.3 Gia công láng:
Đây là công đoạn cần thực hiện đối với những chi tiết yêu cầu cần có độ chính xác và độ nhẵn cao sau khi cắt gọt. Sau khi được gia công láng sản phẩm bị lấy đi một lớp dư gia công rất mỏng, giúp sản phẩm có độ chính xác và độ nhẵn bề mặt cao nhất
10. Chi tiết máy được lắp ghép như thế nào?
Chi tiết máy được lắp ghép với nhau bằng nhiều cách và chúng cũng sẽ tùy thuộc vào yêu cầu kỹ thuật với điều kiện sử dụng. Có thể chia mối ghép chi tiết máy thành hai loại chính là: mối ghép cố định và mối ghép động.
Mối ghép động: Đây là một phương pháp ghép các chi tiết trong máy mà cho phép chúng có thể chuyển động tương đối với nhau. Mối ghép động làm cho các chi tiết đó có thể di chuyển hoặc xoay mà không gây hại đến cấu trúc hoặc hoạt động của máy. Điều này cho phép máy hoạt động một cách linh hoạt và hiệu quả.
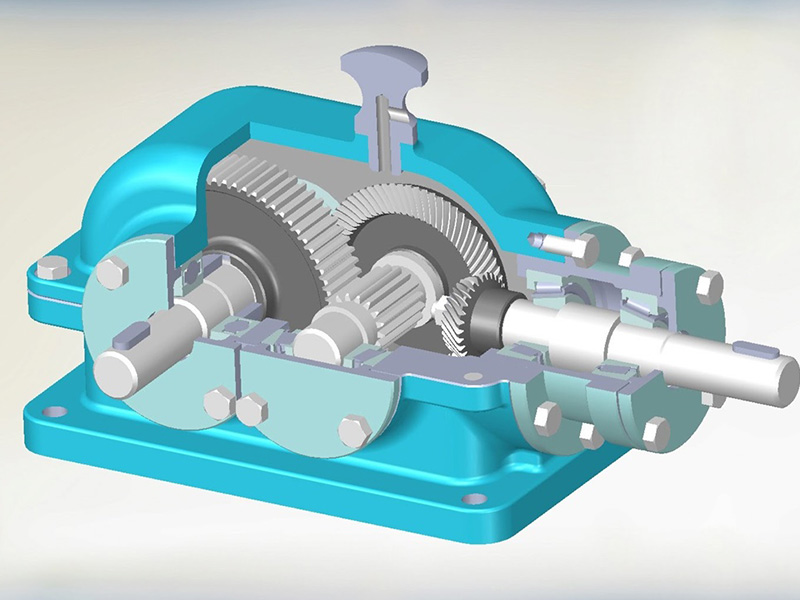
Mối ghép cố định: Là phương pháp ghép các chi tiết trong máy mà chúng không có chuyển động tương đối với nhau. Mối ghép cố định được sử dụng để gắn chặt các chi tiết lại, làm cho chúng không thể di chuyển hoặc xoay. Có hai loại mối ghép cố định là mối ghép tháo được và mối ghép không tháo được.
11. Tiêu chuẩn khi gia công các chi tiết
![]() | ![]() |
Một chi tiết được sử dụng phải đảm bảo các yếu tố kiểm duyệt nghiêm ngặt
Để xác định được chi tiết có đáp ứng yêu cầu hay không, chúng sẽ phải đảm bảo các tiêu chí sau:
11.1 Khả năng làm việc
Một chi tiết máy đạt chuẩn phải đảm bảo đúng chức năng của nó. Ví dụ như một chiếc bánh răng phải đảm bảo khả năng ăn khớp với các bánh răng khác cũng như có thể quay quanh trục ổn định. Khả năng làm việc của chi tiết sẽ được xác định dựa trên những tiêu chí đã đặt ra ban đầu.
11.2 Độ tin cậy
Độ tin cậy của chi tiết được xác định bằng độ bền và độ ổn định khi nó hoạt động trong điều kiện khắc nghiệt nhất trong dự tính. Từ đó, chúng ta sẽ xác định được xem chi tiết này có đảm bảo để vận hành thực tế hay không.
11.3 Sự an toàn trong quá trình sử dụng
Độ an toàn luôn là một trong những yếu tố quan trọng để đánh giá một chi tiết máy. Thực tế là khi một chi tiết máy có độ tin cậy cao và khả năng làm việc đúng như yêu cầu thì gần như nó sẽ luôn đảm bảo sự an toàn. Một số trường hợp đặc biệt, người ta sẽ thiết kế thêm các chi tiết để tăng tính an toàn khi chi tiết vận hành.
11.4 Công nghệ
Tiêu chuẩn công nghệ thường được áp dụng với các chi tiết đặc biệt ứng dụng công nghệ cao. Để đảm bảo tính công nghệ, người ta sẽ cần phải kiểm tra kỹ và tỷ mỷ với các máy móc hiện đại.
11.5 Tính kinh tế
Một chi tiết cần phải có tính kinh tế tối ưu nhất nhằm giảm đi giá thành của sản phẩm đến tay người tiêu dùng. Một chi tiết có tính kinh tế càng cao sẽ càng đảm bảo tính cạnh tranh khi trở thành thành phẩm.